Daihatsu 5DK-20 crankshaft has been successfully repaired by RA Power Solutions technicians on board a vessel recently. A leading shipping company based in Greece operating more than fifty container vessels approached RA Power Solutions to repair the crankshaft of Daihatsu 5DK-20 on the vessel.
The main challenge was that the crankpin no. 03 of Daihatsu 5DK-20 met with a serious accident damaging the radius fillet of both sides of the crankpin. They had a stopover of only 18 hrs at Mundra Port India.
In fact, the owners disparately tried to get the crankpin repaired in Dubai and approached leading companies but none of them was able to repair the crankpin with a damaged radius filet.
Major Technical Details Of Daihatsu 5DK-20 Crankshaft
S. NO | Crankshaft Details | |
1. | Engine Make | Daihatsu |
2. | Engine Model | 5DK-20 |
3. | Crankpin Diameter Standard | 170 mm |
4. | Crankpin Bearing Width | 78 mm |
5. | Place of execution of crankshaft repair | Mundra Port India |
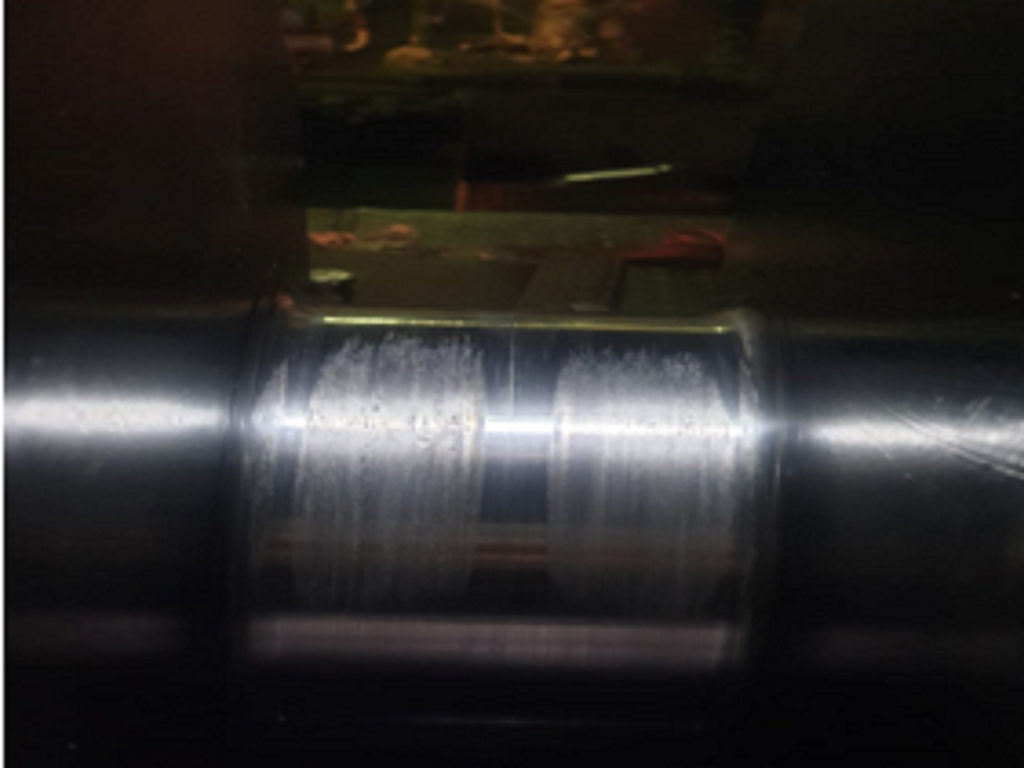
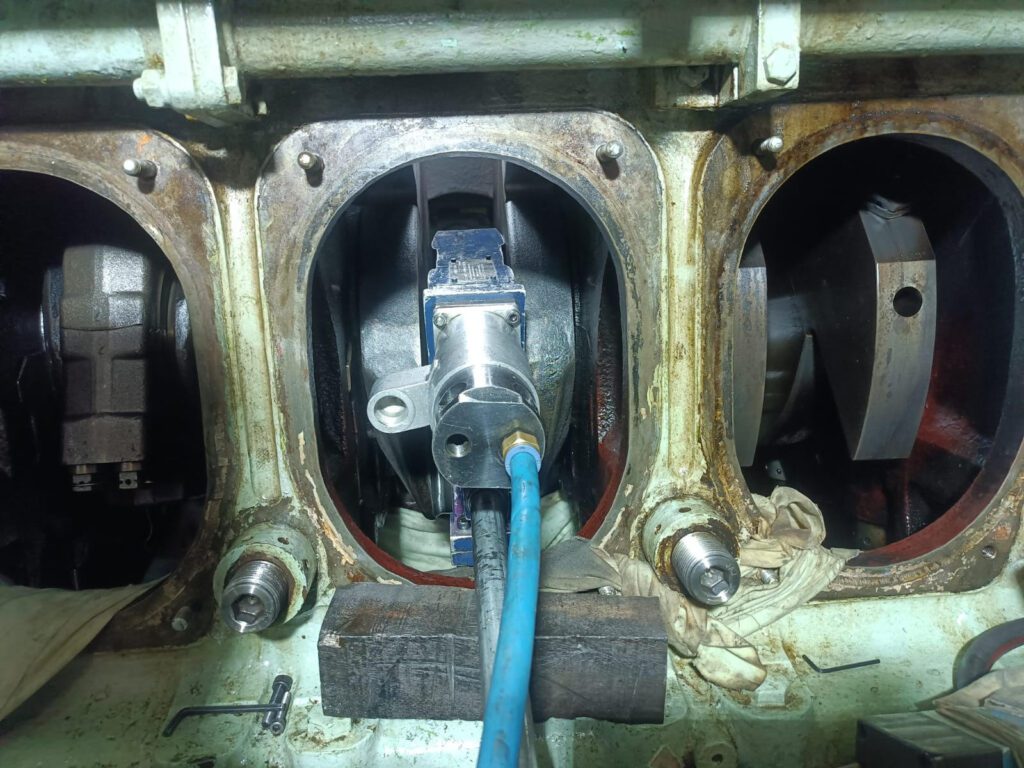
Action taken by RA Power Solutions for successful repair of Daihatsu 5DK-20 Crankpin
- Dimensional inspection of the crankpin no. 03 was done by the technicians and an ovality of 0.49 mm with deep bearing marks, rough surface, etc was observed.
- The radius fillet of both sides of crankpin no. 03 was damaged badly in fact the original profile of the fillet radius of Daihatsu crankshaft was lost due to an accident.
- Hardness and crack detection tests were undertaken and were found within limits.
- Deflection was also within the parameters.
- Our technicians with the help of specially designed compact dedicated tooling for repair of crankpin having small bearing width used the equipment. They reduced the diameter of the crank pin by 1.0 mm and maintained the final diameter of 169.00 mm. Maintaining the tolerance within 0.02 mm, the preparation & formation of radius fillet on both sides of the crank pin was a challenge which was done by our technicians within 18 hours of boarding the vessel.
- In this case of Daihatsu 5DK-20 the crank pin bearing width is only 78 mm and with our specially designed equipment it was possible to undertake the grinding.No other company have the compact tooling to undertake such repairs on site without removing it from the engine block.
- The bearing is only 1.0 mm undersize and was supplied by RA Power Solutions. The engine was commissioned during the presence of our technicians on board the vessel.
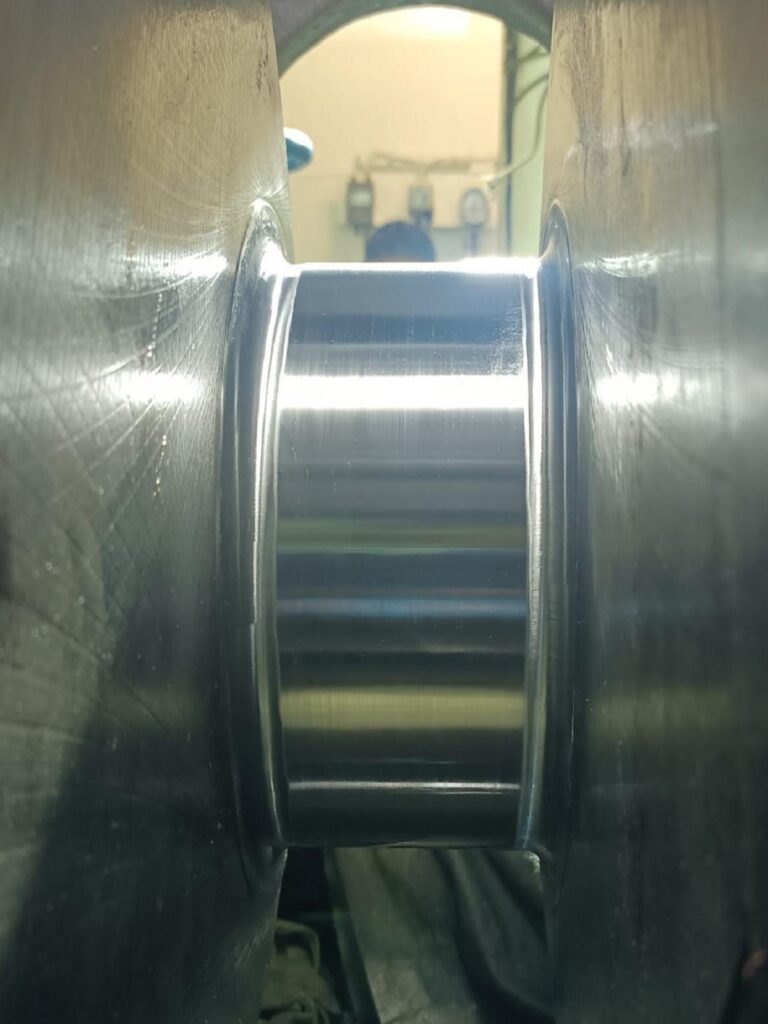
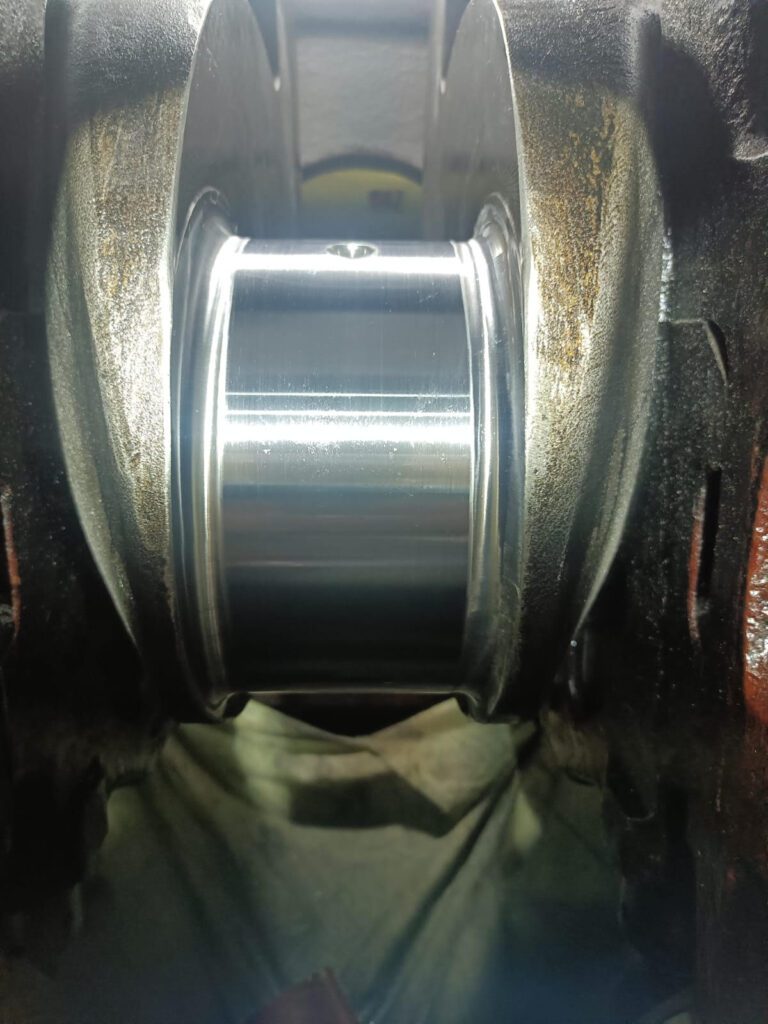
RA Power Solutions is ISO 9001:2015 (Quality Management System) & ISO 14001:2015 (Environmental Management System) certified approved company.
We have been regularly executing onsite crankshaft repairs and crankshaft grinding in Dubai, Oman, Saudi Arabia, Qatar, Abu Dhabi, Sharjah, Ajman, Umm Al-Quwain, and Fujairah, Bahrain, Kuwait, Iraq, Antigua and Barbuda, Belize, Dominica, Dominican Republic, Grenada, Guyana, Haiti, Jamaica, Saint Kitts and Nevis, Saint Lucia, Saint Vincent and the Grenadines, Trinidad, and Tobago, etc.
For more details of the Repair of engine and supply of bearings, Daihatsu 5DK-20 Crankshaft repair please email us on rajshahani@rapowersolutions.com, info@rapowersolutions.com or Call us at +91 9582647131, or +91 9810012383.